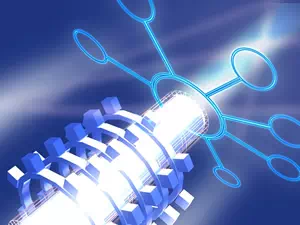
Exposure to certain chemicals can cause or contribute to many serious health effects, including heart ailments, cancer, central nervous system disorders, kidney and lung damage, sterility, burns, and severe skin rashes. Some chemicals may also be safety hazards and have the potential to cause fires and explosions and other serious accidents.
Because of the seriousness of these safety and health problems, and because many employers and employees know little or nothing about them, OSHA has developed a framework called the Hazard Communication Standard (HazCom). The basic goal of the standard is to communicate hazards in the workplace -- to ensure that employers and employees know about work hazards, and know how to protect themselves.
Implementing
the requirements of HazCom provides a great opportunity to continuously educate
staff about choosing or using less chemicals in the first place.
In addition to the Hazard Communication Standard, OSHA has developed a detailed set of rules dealing with specialized topics such as storage of flammable materials, compressed gases (including oxygen), and other materials which are often stored in healthcare facilities. A list of titles, together with link to the text the rules, may be found at the OSHA web site
What is covered under the Hazard Communication Standard (HazCom)?
HazCom covers all chemicals in the workplace. It establishes uniform requirements to make sure that the hazards of each of these chemicals are evaluated, and that this hazard information is transmitted to employers who deal with the chemicals and to employees who might be exposed to them.
Note first that this applies to all hazardous chemicals. The HazCom covers both physical hazards (such as flammability) and health hazards (such as irritation, lung damage, and cancer). Most chemicals used in the workplace have some hazard potential, and thus will be covered by the rule.
How does the HazCom work?
Chemical manufacturers and importers are responsible for evaluating the hazards of the chemicals they produce or import. Using that information, they must then prepare labels for containers, and more detailed technical bulletins called material safety data sheets (MSDSs) discussed below.
Employers that “use” hazardous chemicals must have a program to ensure that this information is provided to potentially exposed employees. “Use” means to package, handle, react, or transfer. This is an intentionally broad scope, and includes any situation where a chemical is present in such a way that employees may be exposed under normal conditions of use or in a foreseeable emergency.
In other words, your chemical supplier is responsible for ensuring that the appropriate evaluation has been performed and that the material is available to you, but you (as a healthcare facility) are responsible for making sure you have obtained the information and have communicated it to anyone in your workplace who may be affected by it.
One difference between this rule and many others adopted by OSHA is that this one is performance-oriented. That means you have the flexibility to adapt the rule to the needs of your workplace, rather than having to follow specific rigid requirements. It also means that you have to exercise more judgment to implement an appropriate and effective program.
Are you located in a "State Plan" State?
If you are operating in a state with an OSHA-approved State Plan, you must comply with your State's requirements, which may be different from those of the Federal rule. Many of the "State Plan" States had hazard communication or “right-to-know” laws prior to promulgation of the federal rule. Employers in State Plan States should contact their State OSHA Offices for more information regarding applicable requirements.
The remainder of this section describes how to prepare a written hazard communications program, which is a key requirement of the Hazard Communication Standard. Other sections in Managing Hazardous Materials cover important elements such as purchasing materials, inventory control, labeling, storage, and materials segregation. These practices will help you comply with the rules in a cost effective manner. Also, there is a list of additional resources that may further improve your understanding of these rules and assist with compliance.
- Written Hazard Communication Program
- Identifying Responsible Staff
- Hazard Inventory
- MSDS Collection and Availability
- Labels and Other Forms of Warning
- Training
Written hazard communication program
Employers must develop, implement, and maintain at the workplace a written, comprehensive hazard communication program. The written plan should include:
- who is responsible for the various aspects of the program in your facility,
- a list of hazardous chemicals in the workplace (hazard inventory),
- how the requirements for labels and other forms of warning, materials safety data sheets, and employee information and training, are going to be met in your facility.
The written program does not have to be lengthy or complicated. Some healthcare facilities may be able to start with an existing written program from another facility and adapt it to their own facility. Several example programs can be found under More Resources
Although these examples may be helpful, you must remember that the written program has to reflect what you are actually doing in your workplace. You can use the example as a basis to get you started, but expect to do some rewriting. You will need to adapt it to address the specific circumstances in your facility. It is not a good idea simply to write up the plan, and then to file it away and forget it. The regulations specify that your written program must be available to
- employees and their designated representatives
- the Assistant Secretary of Labor for Occupational Safety and Health (i.e. to the OSHA inspector, if he or she requests it)
- the Director of the National Institute for Occupational Safety and Health (NIOSH)
In addition, in states with state plans, you may also be asked to make your program available to the appropriate state authorities. It is worth the effort to review the plan periodically to make sure it covers any changes that may have occurred in your facility or your range of operations. At a minimum, that will make it more likely that your staff will know where to find the written plan if someone asks to see it.
The rest of this section deals with several specific topics that your written hazard communications program must address, including:
- Identifying Responsible Staff
- Hazard Inventory
- MSDS Collection and Availability
- Labels and Other Forms of Warning
- Training
Each of these items is covered in more detail in the following paragraphs.
Compliance with HazCom is not a "one shot deal". Hazard communication is a continuous program in your facility. In order to have a successful program that will both protect your employees and pass inspections, you must assign responsibility to specific individuals. This applies both to the initial activities (plan writing and getting the facility into compliance in the first place) and to ongoing activities.
In some cases, these activities may be part of current job assignments. For example, Site Supervisors are frequently responsible for on-the-job training sessions. If you identify which employees will be responsible for implementing the plan and get them involved early in the program design process, your plan will be carried out more effectively. You will also get feedback that will help you evaluate the program.
For any safety and health program, success depends on commitment at every level of the organization. This is particularly true for hazard communication, where success requires a change in behavior. This will occur only if employers understand the program and are committed to its success, and if the people presenting the information motivate employees.
You can refer to the written program examples listed below for ideas on establishing roles and responsibilities.
As part of your written hazard communication program, the standard requires you to prepare a list of all of the hazardous chemicals in the workplace. The list will eventually serve as an inventory of everything for which you must maintain an MSDS. But even from the outset, preparing the list will help you complete the rest of the program, since it will give you some idea of the scope of the program required for compliance in your facility.
The best way to prepare a comprehensive list is to survey the workplace. Purchasing records are also useful for establishing what chemicals have entered the facility "officially". You should of course review them, create a list, and determine the fate of all purchased chemicals once they have been received. But materials also have a way of coming into facilities under the radar (as vendor samples, for example). There is no substitute for actually walking through the facility, clipboard in hand, looking in all the nooks and crannies, and taking copious notes.
During the survey, try to take a comprehensive look around:
- Identify the chemicals in containers but also remember HazCom covers chemicals in all physical forms, liquids, solids, gases, vapors, fumes, and mists whether they are 'contained' or not.
- Think also about chemicals that may be generated during facility operations. For example, welding fumes, dusts, and exhaust fumes are all sources of chemical exposures.
- Read labels provided by the suppliers on hazard information.
- Make a list of all chemicals in the workplace that are potentially hazardous.
Doing
a chemical inventory is a great time to identify hazardous chemicals to reduce
or better yet, eliminate. As you put the inventory together, highlight chemicals
to go back and research for possible alternatives.
Your
first inventory, be prepared to find old or perhaps abandoned chemicals. Are
there chemicals you would remove if you found them? Have a plan in place to
remove unwanted or potentially harmful chemicals. Take pictures and good notes
if you need to go back to collect the waste.
For your own information and planning, you also may want to note on the list the location(s) of the products within the workplace, and an indication of the hazards as found on the label. This will help you as you prepare the rest of your program. To determine whether a particular chemical is covered by the rule, you should consider two factors:
- Can the chemical pose a hazard under any plausible circumstances?
- What is the potential that someone in the workplace might be exposed to the chemical?
If the chemical is inherently non-hazardous, it is not covered (water, mild solutions of innocuous substances, etc.).
MSDS collection and availability
MSDS Inventory
THERE ARE MANY ELECTRONIC MSDS Management systems available. The requirement is that every employee must have access to every MSDS for every chemical found in the area. That requires that ALL staff are properly trained to use the system. If this is not reasonable, you MUST have hard copies available in a format that are easily found, e.g., filed alphabetically. |
Once you have compiled as complete a list as possible of the potentially hazardous chemicals in the workplace, the next step is to determine if you have received material safety data sheets for all of them. Check your files against the inventory you have just compiled. If any are missing, contact your supplier and request one. It is a good idea to document these requests, either by copy of a letter or a note regarding telephone conversations.
If you have MSDSs in your files for chemicals that are not on your list, figure out why. Maybe you don't use the chemical any more. Or maybe you missed it in your survey. Some suppliers do provide MSDSs for products that are not hazardous. These do not have to be maintained by you. If you have questions regarding the hazard status of a chemical, contact the manufacturer, distributor, or importer.
You should not allow employees to use any chemicals for which you have not received an MSDS. The MSDS provides information you need to ensure you have implemented proper protective measures for exposure.
Having gone through this exercise once, you will not want to have to repeat it too often. You will find it advantageous to have procedures in place to confirm that the appropriate MSDS has been received for every new chemical and is on file in the right location before any material your facility receives is released for use in the workplace.
What is an MSDS? The MSDS is a detailed information bulletin prepared by the manufacturer or importer of a chemical that describes the physical and chemical properties, physical and health hazards, routes of exposure, precautions for safe handling and use, emergency and first-aid procedures, and control measures. Chemical manufacturers and importers must develop an MSDS for each hazardous chemical they produce or import, and must provide the MSDS automatically at the time of the initial shipment of a hazardous chemical to a downstream distributor or user. Distributors also must ensure that downstream employers are similarly provided an MSDS.
Each MSDS must be in English and include information regarding the specific chemical identity of the hazardous chemical(s) involved and the common names. In addition, information must be provided on the physical and chemical characteristics of the hazardous chemical; known acute and chronic health effects and related health information; exposure limits; whether the chemical is considered to be a carcinogen by NTP, IARC, or OSHA; precautionary measures; emergency and first-aid procedures; and the identification (name, address, and telephone number) of the organization responsible for preparing the sheet. Copies of the MSDS for hazardous chemicals in a given work site are to be readily accessible to employees in that area. As a source of detailed information on hazards, they must be readily available to workers during each work shift.
Personnel Protective Equipment (PPE)
HazCom best management practices dictate that the employer must make available and communicate the proper and specific PPE to be used when handling specific hazardous chemicals. Specific procedures must be outlined and clearly articulated by the employer to provide protection such as engineering controls, best work practices, and the use of personal protective equipment (PPE).
Likewise, PPE for spills and management of hazardous wastes must also be made available and communicated.
Proper labeling of hazardous chemical and waste is extremely important to reduce exposure, prevent accidents and extra disposal costs:.
OSHA's Hazard Communications Program (HazCom) (link) covers the labeling of hazardous chemicals in use. Once the chemical becomes a hazardous waste, a different set of labeling rules apply under EPA's RCRA program (provide link). To add to the challenge of labeling all hazardous materials, to prepare hazardous waste for shipment, another set of rules apply under the Department of Transportation (DOT) (provide link).
HazCom requires that all containers of hazardous chemicals must be labeled, tagged, or marked with the identity of the material and appropriate hazard warnings. Chemical manufacturers, importers, and distributors must ensure that every container of hazardous chemicals they ship is appropriately labeled with such information and with the name and address of the producer or other responsible party.
Additional information on labeling: • Third party labeling systems are available to communicate specific hazards such as toxicity, flammability, reactivity and other hazards. HMIS and NFPA Labeling Systems |
The primary information to be obtained from an OSHA-required label is the identity for the material and appropriate hazard warnings. The identity is any term which appears on the label, the MSDS, and the list of chemicals, and thus links these three sources of information. The identity used by the supplier may be a common or trade name ("Black Magic Floor Cleaner"), or a chemical name (1, 1, 1 - trichloroethane). The hazard warning is a brief statement of the hazardous effects of the chemical ("flammable," "causes lung damage"). Labels frequently contain other information, such as precautionary measures ("do not use near open flame") but this information is provided voluntarily and is not required by the rule.
Labels must be legible and prominently displayed. There are no specific requirements for size or color or any specified test.
Proper labeling is extremely important to prevent accidents and extra disposal costs
- Ensure proper labeling of all incoming materials as they are received (Include product name, weight, concentration, lot number, date, hazard class and any other information useful in tracking material location, quality, age or use.)
- Always label hazardous waste at its point of generation where it can still be easily identified (Testing later to determine the contents is expensive.)
- Label all areas in the plant, including stationary tanks, pipelines, etc. containing hazardous materials or wastes
- If a chemical was in a labeled container and is subsequently transferred to another container, the employer must label the new container.
- Shelving where the chemical is stored may be labeled with additional labeling if when the chemical is removed from the labeled shelf, it will be used in its entirety. If not, it will require an additional label.
Specifically, HazCom requires the following types of information to ensure that labeling is properly implemented in your facility:
- Designation of person(s) responsible for labeling system implemented throughout the facility;
- Designation of person(s) responsible for ensuring labeling of all containers in each department/area;
- Designation of person(s) responsible for ensuring re-labeling of hazardous waste or to prepare waste for shipping
- Description of labeling system(s) used and comprehensive training program;
- Description of written alternatives to labeling of containers (if used); and,
- Procedures to review and update label information when necessary.
Employers must establish a training and information program for ALL new employees as part of orientation and an ongoing program for all employees may be are exposed to hazardous chemicals in their work area at the time of initial assignment and whenever a new hazard is introduced into their work area. At a minimum, the discussion topics must include the issues outlined below.
New employee
orientation is the first opportunity to communicate to new staff your facility's
commitment to using hazardous chemicals safely and minimizing or eliminating
their use at every opportunity. Encourage their participation in these efforts.
- How the hazard communication program is implemented in that workplace, how to read and interpret information on labels and the MSDS, and how employees can obtain and use the available hazard information.
- The hazards of the chemicals in the work area. (The hazards may be discussed by individual chemical or by hazard categories such as flammability.) Operations in work areas where hazardous chemicals are present and measures employees can take to protect themselves from the hazards.
- Specific procedures put into effect by the employer to provide protection such as engineering controls, work practices, and the use of personal protective equipment (PPE).
- Methods and observations, such as visual appearance or smell, workers can use to detect the presence of a hazardous chemical to which they may be exposed.
- Training to protect workers in the event of a spill or leak of a hazardous chemical from a sealed container.